working principle
When the laminated filter works normally, water flows through the laminated filter, using the wall and groove to gather and intercept debris. The composite inner section of the groove provides three-dimensional filtration similar to that produced in sand and gravel filters. Therefore, its filtration efficiency is very high. When the laminated filter is working properly, the laminated filter is locked. The filter is also movable or automatically flushed. When manual washing is required, remove the filter element, loosen the compression nut, and rinse with water. At the same time, it is stronger than the net filter retention of impurities, so the number of washing is relatively less, washing water consumption is smaller. However, the laminated sheet must be loose by itself when automatic washing. Because of the influence of organic matter and chemical impurities in the water body, some laminated sheets are often stuck together and not easy to be thoroughly washed.
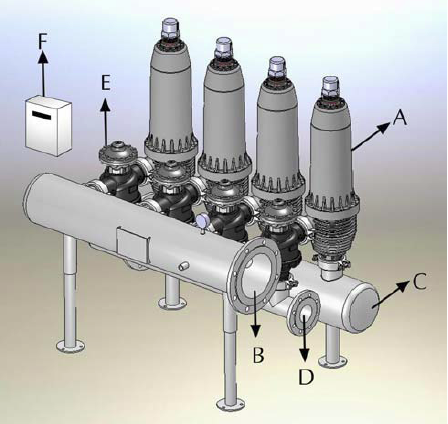
Working Process
When the laminated filter works normally, water flows through the laminated filter, using the wall and groove to gather and intercept debris. The composite inner section of the groove provides three-dimensional filtration similar to that produced in sand and gravel filters. Therefore, its filtration efficiency is very high. When the laminated filter is working properly, the laminated filter is locked. The filter is also movable or automatically flushed. When manual washing is required, remove the filter element, loosen the compression nut, and rinse with water. At the same time, it is stronger than the net filter retention of impurities, so the number of washing is relatively less, washing water consumption is smaller. However, the laminated sheet must be loose by itself when automatic washing. Because of the influence of organic matter and chemical impurities in the water body, some laminated sheets are often stuck together and not easy to be thoroughly washed.
Filtration
Water flow through the filter inlet into the filter, filter stack is tightly pressed together by the filter stack under the action of spring force and hydraulic power, impurity particles are intercepted in the stack crossing point, filtered water flows out of the main channel of the filter, at this time the one-way diaphragm valve is open.
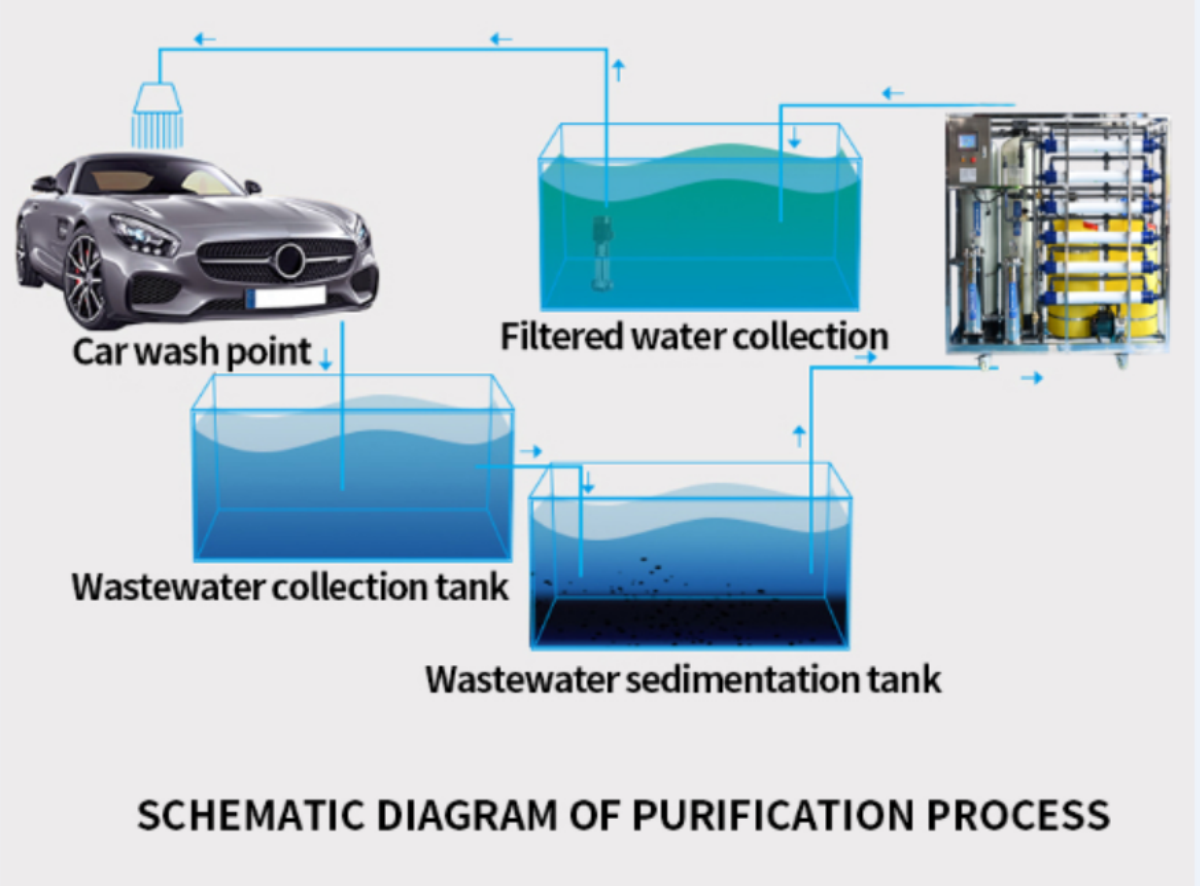
Backwash
When a certain pressure difference is reached, or the set time, the system automatically enters the backwash state, the controller controls the valve to change the direction of water flow, the one-way diaphragm at the bottom of the filter closes the main channel, the backwash enters the four groups of nozzle channel, and the nozzle channel connected with the piston chamber of the water pressure rises, the piston moves upward to overcome the spring pressure on the stack, and releases the piston space at the top of the stack. At the same time, the backwashing water is sprayed at high speed from 35*4 nozzles above the four groups of nozzle channels along the direction of the tangent line of the stack, so that the stack rotates and evenly separated. The washing water is sprayed to wash the surface of the stack, and the impurities intercepted on the stack are sprayed and thrown out. When the backwash is complete, the flow direction changes again, the laminate is compressed again, and the system re-enters the filtration state.
Technical Parameter
Shell material | lined plastic steel pipe |
Filter head housing | reinforced nylon |
Laminated material | PE |
Filter area (laminated) | 0.204 square meters |
Filtration accuracy (um) | 5, 20, 50, 80, 100, 120, 150, 200 |
Dimensions (height and width) | 320mmX790mm |
Working pressure | 0.2MPa -- 1.0MPa |
Backwash pressure | ≥0.15MPa |
Backwash flow rate | 8-18m /h |
Backwash time | 7 -- 20S |
Backwash water consumption | 0.5% |
Water temperature | ≤60℃ |
Weight | 9.8kg |
Product advantages
1.Precise filtration: Filter plates with different precision can be selected according to water requirements, including 20 micron, 55 micron, 100 micron, 130 micron, 200 micron, 400 micron and other specifications, and the filtration ratio is greater than 85%.
2. Thorough and efficient backwashing: Because the filter pores are completely opened during backwashing, coupled with centrifugal injection, the cleaning effect can not be achieved by other filters. The backwash process takes only 10 to 20 seconds per filter unit.
3.Full automatic operation, continuous water discharge: time and pressure difference control backwash start. In the filter system, each filter unit and workstations are backwashed in sequence. Automatic switching between working and backwashing states can ensure continuous water discharge, low pressure loss of the system, and the effect of filtration and backwashing will not deteriorate due to the use time.
4.Modular design: Users can choose the number of parallel filter units according to demand, flexible and changeable, strong interchangeability. Flexible use of site corner space, according to local conditions less installation area.
5.Simple maintenance: almost no need for daily maintenance, inspection and special tools, few detachable parts. The laminated filter element does not need to be replaced, and the service life can be up to 10 years.
Application Field
1.Full filter or side filter of circulating water of cooling tower: it can effectively solve the problem of circulating water blockage, reduce energy consumption, and reduce the dosage, prevent failure and shutdown and reduce system maintenance costs.
2.Reclaimed water reuse and sewage pretreatment: save the total amount of water, improve the quality of water used, reduce or avoid the pollution caused by direct sewage discharge to the environment.
3.Desalination pretreatment: remove impurities and Marine microorganisms from seawater. The salt resistance and corrosion resistance of plastic filter is better than that of other more expensive metal alloy filter equipment.
4.Primary filtration before ultrafiltration and reverse osmosis membrane treatment: to protect the precision filter element and extend its service life.
Besides, laminated filters are widely used in : chemical industry, electric power, steel, machinery manufacturing, food and beverage processing, plastics, paper, mining, metallurgy, textile, petrochemical, environment, golf course, automobile, tap water front filter.